Exploring the Future of Precision Steel Ball Manufacturing: Innovations and Trends
- Zihan Chen
- Dec 25, 2024
- 3 min read
The precision steel ball manufacturing industry is experiencing a remarkable transformation. Driven by technological advancements, changing consumer preferences, and an increasing need for efficiency, this sector is poised for significant growth. As industries, from automotive to aerospace, evolve, precision steel balls play a critical role in applications where precision and reliability are crucial. In this post, we will explore the future trends in precision steel ball manufacturing and highlight the innovations defining this industry.
Current Landscape of Precision Steel Ball Manufacturing
To understand the future, we must first examine the current state of precision steel ball manufacturing. Traditionally, manufacturers relied on a mix of manual labor and mechanized systems to produce steel balls. In recent years, however, automation and advanced manufacturing techniques have gained ground.
For example, the use of automated systems for sorting and inspection has become common. This shift not only lowers labor costs but also boosts production efficiency and product quality consistency. In fact, manufacturers can now achieve production increases of up to 30% while reducing lead times through automation, demonstrating the impact of these innovations.
Technological Innovations Driving Change
Technological advancements are reshaping precision steel ball manufacturing. Various cutting-edge processes are transforming production capabilities.
Additive Manufacturing: This technology allows manufacturers to produce intricate designs that were previously unattainable with traditional methods. For instance, using 3D printing, companies can create custom steel balls suited for specialized applications, such as those needed in specific aerospace components. This adaptability is vital as industries increasingly seek tailored solutions.
CNC Machining: Computer Numerical Control (CNC) machining provides exceptional precision in manufacturing. By automating tasks like cutting and shaping, manufacturers can achieve tighter tolerances. This increases the quality of steel balls produced, allowing for reductions in defects to as low as 0.1%.
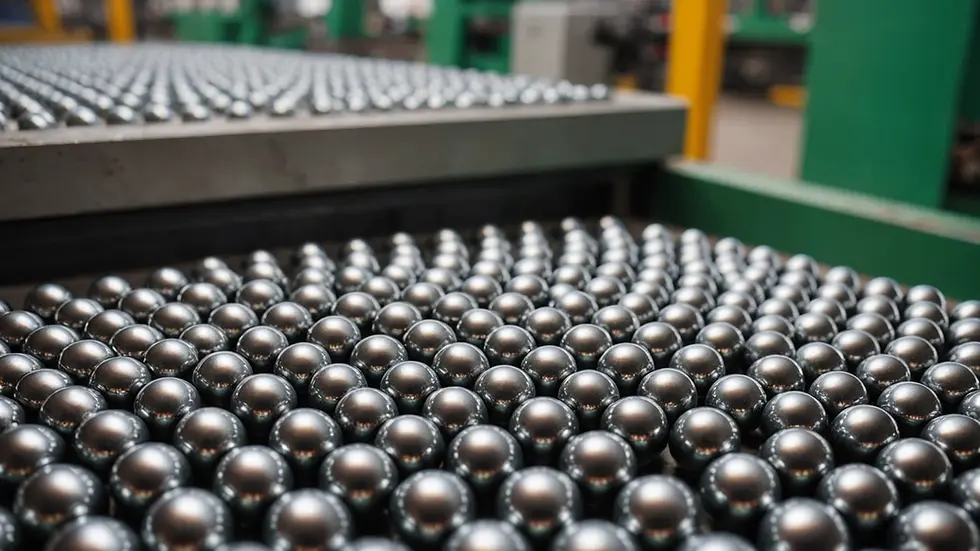
Focus on Sustainability
Sustainability is a growing concern across all industries, including precision steel ball manufacturing. Increasing awareness of environmental impacts encourages manufacturers to re-evaluate their practices.
Many companies are now using recycled steel and implementing energy-efficient processes. For example, a recent study found that manufacturers adopting cleaner production techniques reduced their carbon footprints by up to 20%. This endeavor not only helps the planet but also attracts eco-conscious consumers who are willing to pay more for sustainable products.
The Role of Globalization
Globalization significantly influences the precision steel ball manufacturing sector. As companies expand their markets, establishing efficient global supply chains is vital. Being able to source materials from different regions enables businesses to lower production costs and adapt quickly to changing demand.
However, globalization poses challenges as well. Companies must navigate tariffs and international trade regulations. Staying informed about global market trends and adjusting strategies accordingly is essential for maintaining competitiveness.
Customization and Market Demand
The demand for customized precision steel balls is increasing as industries seek specialized products for specific uses. This trend is particularly strong in automotive, aerospace, and medical device sectors, where precision often determines safety and reliability.
Manufacturers are investing heavily in research and development to meet this need. Collaborative efforts with clients lead to tailored solutions that enhance satisfaction and foster long-term partnerships. For example, custom-designed steel balls can improve the efficiency of engine components, directly impacting vehicle performance and customer satisfaction.
Industry 4.0: Smart Manufacturing
Industry 4.0 is transforming the landscape of precision steel ball manufacturing. The integration of the Internet of Things (IoT), big data analytics, and artificial intelligence is streamlining production processes.
With connected devices collecting real-time data, manufacturers can optimize equipment performance and anticipate maintenance needs. According to industry reports, implementing these technologies can enhance operational efficiency by up to 25%. This not only minimizes downtime but also elevates quality control, ensuring products consistently meet the highest standards.
Challenges Ahead
Despite the promising future of precision steel ball manufacturing, challenges persist. The complexity of modern manufacturing processes requires a skilled workforce trained to operate advanced machinery.
Additionally, the fluctuating costs of raw materials and the need for stable supply chains remain ongoing concerns. Companies must commit to investing in staff training and devising robust risk management strategies to navigate these challenges successfully.
A Look Ahead
The future of precision steel ball manufacturing hinges on innovation, adaptability, and sustainability. As technological advancements continue to reshape the industry, manufacturers must proactively respond to evolving consumer demands and market dynamics.
By embracing customization, prioritizing eco-friendly practices, and leveraging smart manufacturing principles, the precision steel ball sector can thrive in a competitive landscape. As we look forward, the integration of innovative technologies along with a commitment to quality will be essential in steering this crucial industry towards a successful future.
Comments